Web-Based Software Tool for Roll-to-Roll (R2R) CM Systems
Mentor: P.R. Pagilla, Mech. Eng.
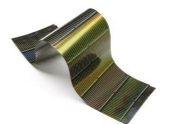
Flexible solar panel
Background: Roll-to-Roll (R2R) manufacturing is an efficient and scalable method to manufacture many consumer products from flexible materials usually referred to as webs. It offers significant advantages over batch manufacturing, including high speed automation and mass production of finished materials at substantially lower costs. It has been extensively used in the paper and sheet metal industry for over a hundred years, and in the last several decades in the production of flexible plastics and polymers. The need to develop new and efficient R2R technologies for new products is rapidly increasing. In particular, recent advances in nanotechnology and advanced materials and processes is enabling R2R manufacturing of a wide variety of consumer electronic products, including flexible panel displays, photovoltaics, engineered surfaces, and flexible solar films.
Research Objectives: The goal of this REU project is to develop a simple web-based software tool to predict the lateral motion of a flexible material on rollers in R2R machines in a CM environment. Control of lateral motion of the moving web is critical in all R2R processes as it enables efficient transport on rollers through the machine. The web-based software tool will provide the user the ability to input a R2R machine web path configuration. Based on lateral dynamic models that predict lateral motion of the web on rollers, the software tool will provide guidelines for location of web guide mechanisms that are used to control the lateral position of a moving web on rollers. The project will initiate a much needed effort in developing such web-based tools that can be accessed by the R2R user community. Large web manufacturers, such as 3M, DuPont, and Proctor and Gamble, have custom software tools for their R2R machines and processes. However, converting the industry which uses R2R machines to convert webs to value-added products such as labels, filters, screens, etc., do not have access to such tools. Therefore, this project fills this gap, and enables the underlying effort in CM.
Research Plan: REU students will learn the concepts involved in transport behavior of moving webs in R2R machines, an ability to analyze and simulate dynamic models of web transport behavior, and engage in experimental evaluation on a modular R2R machine that can be configured for different web paths. Details of the R2R machine are provided in the facilities section of the proposal. The student will conduct the basic model analysis to predict lateral motion resulting from various processes and machine induced disturbing forces, which will lead to recommendations on the placement of web guide mechanisms in the R2R machine to improve lateral transport behavior and obtain quality wound rolls. The ability to experimentally evaluate the analysis conclusions on the modular R2R machine platform will provide valuable hands-on experiences for the student. The student will interact with other students in R2R manufacturing, and trained graduate students are available to provide mentoring to the undergraduate student.
Student Outcomes: The results of the project will be presented by the student at conferences and local symposia. Dr. Pagilla has successfully engaged undergraduate students in R2R research in other funded NSF projects, and those experiences will be leveraged to provide a valuable research experience (including co-authorship with graduate students in journal article) to the undergraduate student on this project.
Cyber-Physical System for Kirigami Based Manufacturing
Mentors: A. Srinivasa, Mech. Eng., and P.R. Kumar, Elec. & Comp. Eng.
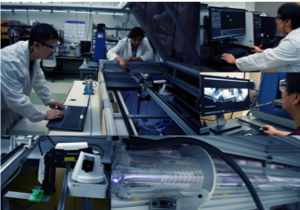
TAMU Kirigami manufacturing system
Background: The idea of an autonomous kirigami cybermanufacturing system (AKCS) is to be able to cut and fold (kirigami) polymeric sheets for making custom components, somewhat like how photocopiers operate. Such a system has the potential to revolutionize the designer/maker movement by providing access to custom precision manufacturing from any computer. This research aligns with TEES IMS thrusts in creating hybrid machines based CM environment.
Research Objectives: Our objective is to identify and investigate the key scientific and technological aspects of an AKCS system. A proof-of-concept machine tool to be developed from the proposed research will serve as a test bed and its performance would be compared and benchmarked with hybrid and other 3-D printing machines. The developed test bed will be used to create a local CM testbed within TAMU.
Research Plan: In addition to helping assemble a prototype laser kirigami machine, the REU students will work alongside graduate student researchers engaged in an NSF EAGER: Cybermanufacturing project on how to convert a virtual part that is built as a sequence of cut and fold operations into a set of machine instructions that is verifiably compatible with a given machine (process planning). These tasks will involve developing the test bed consisting of a laser cutter with an indexer and single point incremental forming tool, instrumenting the laser machine tool with sensors, and developing computer control interfaces to carry out kirigami operations.
Student Outcomes: Students will learn the interplay between physical modeling, process planning and control which is likely to be at the heart of cybermanufacturing, and—more broadly—the internet of things. We expect the REU students to co-author at least one article to an archival journal and create at least one poster for the USRG program.
A Cyber-Physical Systems Approach for Prognostication in Custom-Manufacturing Processes
Mentors: S. Bukkapatnam, Industrial & Sys. Eng., and P.R. Kumar, Elec. & Comp. Eng
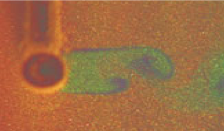
A thermochromics-embedded sheet precursor that reversibly changed color with temperature during a forming operation. This effect can be used to track a custom process.
Background: This recently approved EAGER: Cybermanufacturing project investigates a radically new approach for real-time process control in custom manufacturing based on combining recent advances in CPS technologies, image analysis (e.g., fast digital image stereo correlation, DISC), passive wireless sensing, and real-time adaptation. We envisage custom manufacturing machines operating standalone in cloud-connected kiosks (e.g., within stores like Home Depot), operated by a non-technical workforce (somewhat like a photocopier at Kinkos) to enable broad retail customer use. A major challenge to this vision is to alleviate the high cost of quality loss in 3-D printing (both sheet and powder based processes). As noted earlier, fault monitoring and control as well as process planning for one-of-a-kind or low volume manufacturing become critical needs. While mass production systems can be progressively improved/optimized over time using repetitive or iterative control strategies, they are not suitable for custom manufacturing where each part requires unique motion and parameter setting. Close proximity sensing and the ability to relate sensor data to the underlying process mechanics is essential. Also, change anticipation (as opposed to mere detection) is necessary to building resilience to disruptions in manufacturing systems that have inherent lag and/or inertia, and thus prevent quality loss. Sensing and real time prediction of future states and “change detection” (deviations from predicted states) are the key to effective implementation.
Research Objectives: To address the aforementioned challenges the PIs would investigate novel real-time sensing and control strategies that are fundamentally anticipative. The specific project objective is to investigate the prognostication of impending sheet faults using a novel imaging and control approach.
Research Plan: REU students would work with a group of graduate students on a CNC milling machine equipped with multiple cameras and vibro-acoustic sensors to study an incremental sheet forming process. The proposed tasks are as follows: (i) embedding thermochromic particles in the sheet precursor, (ii) tracking particles’ local motion and distortion using multiple cameras (DISC) as the sheet is being formed to estimate process state, and (iii) applying internal model principles to prognosticate and synthesize anticipatory control laws using the granular process state estimates. The challenge here is different from typical image sensing in that we have the ability to “push” features to the cameras so that change identification may be faster and granular. Following research questions will be addressed in the proposed research: 1) How to anticipate future state from sensor measurements? 2) How to develop control schemes based on the state prediction to prevent and protect the system in the case of some failure (e.g., equivalent of a paper jam), and ensure that custom parts meet specifications? 3) How can image based sensing be used to track and detect faults in a custom manufacturing processes? The proposed work would lead to the development of a test bed to investigate the new control approach.
Student outcomes: The REU students will gain hands-on experience with the instrumentation and operation of machine tools, as well as the implementation of DIC processing methods and data interpretation. The research work spurred from the summer effort will be communicated to a manufacturing journal.
Computer-Communication System for Cybermanufacturing
Mentor: N. Gautam & S. Bukkapatnam, Industrial & Sys. Eng.
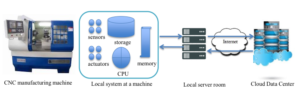
Communication network for cybermanufacturing
Background: The state of the art in cloud-based manufacturing consists of collecting and sending large amounts of data to a cloud data center to perform offline computing for root cause. However, there is a significant need in cybermanufacturing for real-time information exchange between geographically dispersed locations for effectively controlling a process. To enable this, a hybrid approach is necessary with local storage and local processing capability as well as a cloud-based data center to reap the benefits of real-time monitoring and control capabilities. If done right this would create significant improvements to the production systems by managing downtimes, enabling energy savings, reducing wastage, improving predictability, and enhancing decision-making. However, limitations in capacity, uncertainty in communications, and widely varying requirements for manufacturing each product, pose significant challenges in achieving the aforementioned improvements.
Research Objectives: The objective of this research study is to address the above challenges by making appropriate strategic, tactical and operational decisions in the computer-communication system. In particular, strategic decisions include the appropriate computer-communications infrastructure for both local and cloud layers. Once a daily manufacturing plan is created, a tactical decision would be to determine what information needs to be stored and processed locally, and what needs to be sent to the cloud. Then, in real-time the operational decisions include control actions regarding where requests should be sent to and at what granularity they must be processed so that deadlines can be met while not compromising on quality.
Research Plan: Using the data transmitted from a CNC milling machine equipped with multiple cameras and vibro-acoustic sensors to a local computer system, alternatives for the above strategic, tactical and operational decisions will be evaluated by comparing various performance metrics including response times, quality of products and machine utilization. A semi-virtual testbed will be developed to emulate a cloud-based data center virtually connected to the above-mentioned CNC machine and any other machine, which could be at a same or different geographic location. The testbed would be used to verify and validate the decisions. The REU students would calibrate mathematical models developed by graduate students to predict performance metrics and then implement on the semi-virtual testbed.
Student Outcomes: The REU experience will enhance the student’s ability to conduct research, develop modeling and analysis skills, perform computer simulation and physical experiments, and analyze complicated systems with unstructured data. In addition, it would enhance the student’s ability to work in multidisciplinary teams and hone their communications skills. The results from this study would be submitted to a manufacturing conference and a journal.
Enterprise Wide Optimization of Product Design, Manufacturing and Supply Chain Configuration for CM
Mentors: B. Nepal and M.D. Johnson, Eng. Tech. & Ind. Distribution
Background: Highly customized manufacturing is the ultimate goal of CM. To achieve this goal, it is imperative to tackle manufacturing of a product from an enterprise perspective. For example, product architectural characteristics such as size, shape, and nature of interfaces between the components affect the operational decisions in the supply chain domain including customer service level, delivery schedule, vehicle routing, and crew planning. Likewise, manufacturing process-related decisions such as manufacturing lead time, setups, and supply chain decisions (such as supplier selection and inventory placement decisions) are dependent on the structure of the end product. The enterprise-wide optimization strategy carries special significance to CM (which is highly customized like those of shale gas drilling components, or biomedical products) because their costs of downtimes (or quality error) can be extremely high. Using genetic algorithm (GA) and hierarchical optimization techniques, Dr. Nepal and his team have developed fuzzy-logic based multi-optimization models to optimally design the supply chain network by aligning it with the type of product architecture.
Research Objectives: This project aims to quantify the impact of product architecture on the manufacturing and supply chain costs, thereby optimizing the total cost for cybermanufacturing components.
Research Plan: The REU students, working with graduate students, will modify the GA and Fuzzy logic codes to perform the sensitivity analysis in the context of CM. The student will also perform cost and risk analysis studies for different scenarios.
Student Outcomes: i) Understanding the interplay between different enterprise level variables, such as supplier selection, product architecture, and manufacturing decision; and ii) appreciate the central role of manufacturing enterprise in a globalized economy, thereby stimulating the student’s interest in the field of manufacturing. The results of the project will be submitted for refereed publications.
Cyber-Physical Manufacturing of Surgical Simulation Enterprise
Mentor: B. L. Tai, Mech. Eng.
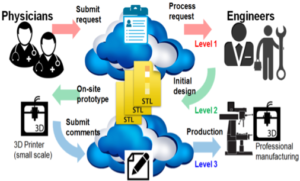
Flowchart for a cloud-based surgical simulator design
Background: Surgical simulators play an important role in medical education and surgical training. Specialized procedures, such as brain or spinal surgery, are often taught on live patients or cadavers. Live training is risky to the patient and time-consuming, which conspires to increase healthcare costs. Cadaver training is also expensive and requires special facilities. Most surgeons prefer a physical, high-fidelity model that they can touch and perform exact procedures for demonstration and training. However, developing such a model takes significant effort and time since it requires collaborative engagement of both engineers and surgeons. In the past, this was possible in only university hospitals with close collaboration with engineering departments.
Research Objective: This project aims to study the feasibility of a cloud-based communication for custom design and manufacturing via rapid prototyping technology (e.g., 3D printing). Figure 8 is a proposed flowchart. Surgeons can upload de-identified patient’s data and specify the needs to design engineers (Level 1). Engineers then come up with a CAD model that can be 3D printed on-site at the hospital for surgeons to review and discuss (Level 2). The finalized model will be sent to engineers for precision manufacturing with desired tolerances and material properties (Level 3). This quick turn-around flow design is anticipated to benefit the healthcare system by providing training and immediate surgical planning.
Research Plan: The REU students will work with Dr. Tai on developing the platform of cloud communication and evaluate the proposed framework using two successful simulation models. The proposed cloud design project can enable remote discussion between surgeons and engineers who use different terminologies. The preliminary validation will be conducted in the PI’s lab. Upon successful development, the PI will reach out to clinicians at Texas Medical Center in Houston to evaluate the feasibility.
Student Outcomes: REU students will learn the skills for CAD design, 3D printing, 3D image processing and visualization. Students will also experience the traditional processes, such as machining and molding, for a customized design. We expect students to generate physical products for use and evaluation, and potential joint publications.